Products
DC Brushless Motor
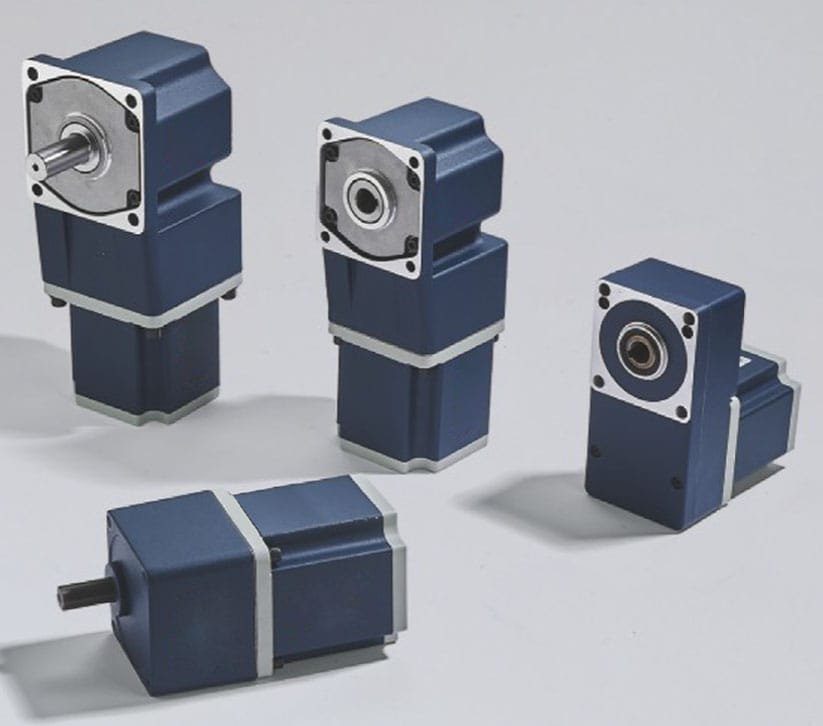
DC brushless motor manufacturer
HM Motor is a manufacturer specializing in the production of DC brushless gear motors. We offer customized brushless motors tailored to applications across various fields, including the 60 Series DC Brushless Gear Motor, 80 Series DC Brushless Gear Motor, 90 Series DC Brushless Gear Motor, and 104 Series DC Brushless Gear Motor. In product research and development, manufacturing, and sales, we consistently lead the industry, and our DC brushless motors have been widely adopted across numerous sectors. As a professional DC brushless gear motor manufacturer, we uphold the principle of “quality first, customer foremost.” Through relentless pursuit of technical excellence and stringent quality control, we provide customers with high-quality brushless motor products that deliver stable performance and reliable quality.
DC Brushless Gear Motor Series
A DC brushless gear motor is a type of DC motor that employs brushless electronic speed control technology. Unlike traditional brushed motors, brushless motors use permanent magnets and power electronics to replace carbon brushes and mechanical commutators, offering advantages such as high efficiency, low noise, long lifespan, and minimal maintenance. Additionally, the motor integrates a gear reducer, which converts the high-speed, low-torque output of the motor into low-speed, high-torque output. This makes it particularly suitable for applications requiring high torque and low-speed operation. Such motors are widely used in fields including robotics, home appliances, medical devices, and automotive applications.
Applications of DC brushless reduction motor
The DC brushless gear motor is a motor characterized by stable performance, smooth operation, and adjustable speed. It is widely applied across various fields, including:
- Robotics and Automation Equipment: Robots and automation systems require high-precision, fast, and low-noise driving forces to accomplish complex tasks.
- Home Appliances: DC brushless gear motors are used in household appliances, providing reliable motor operation for devices such as washing machines, fans, vacuum cleaners, electric shavers, and blenders.
- Medical Devices: In medical equipment, DC brushless gear motors are employed in applications like surgical robots, central oxygen systems, and medical pumps, delivering precise control and long-term reliable performance.
- Automotive and Construction: DC brushless gear motors are also widely utilized in the automotive and construction industries, powering components such as window mechanisms, seat adjustment systems, cranes, and industrial sewing machines, where they provide dependable power and output.
Characteristics of DC brushless reduction motor products
On brushless motors, there is no need to use mechanical contacts such as brushes and rectifiers, which are commonly considered drawbacks of DC motors. DC motors use brushes and rectifiers to rotate, so regular maintenance is required. Brushless motors use signals detected by Hall ICs to rotate using the ON/OFF of transistors in the drive circuit, so no maintenance is needed.
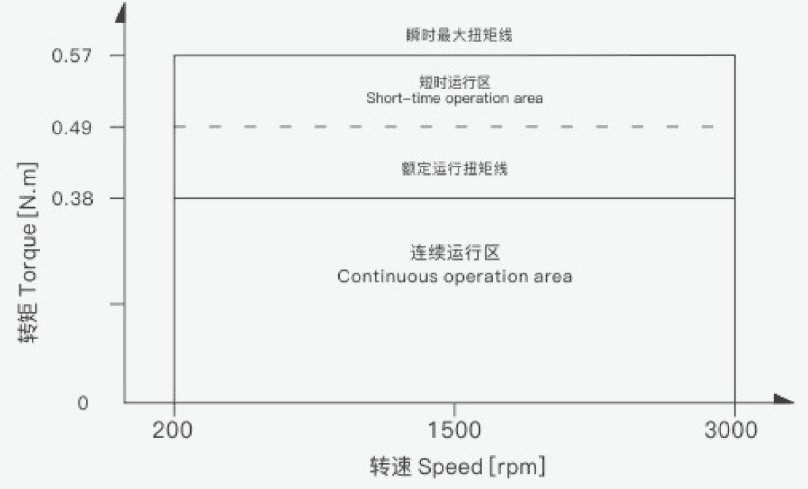
Explanation of characteristic curve of DC brushless deceleration motor
- Instantaneous Maximum Torque Line: The maximum torque during motor startup or instantaneous impact load; exceeding this torque value will trigger the driver’s overcurrent protection, resulting in a shutdown.
- Short-Term Operation Zone: At different motor speeds, the motor can operate briefly within this torque range; prolonged operation may cause the motor to overheat, potentially leading to burnout or triggering the driver’s overheating protection, resulting in a shutdown.
- Rated Operating Torque Line: The rated torque of the motor at different speeds, allowing for long-term operation at this torque level.
- Continuous Operation Zone: At different speeds, the motor can operate continuously within the corresponding range.

Thin and high-power
The rotor of a brushless motor uses permanent magnets, enabling a slim design and high power output. For example, compared to a three-phase induction motor with a mounting size of 90, the total length is reduced by more than 75mm, while the output power increases to 1.3 times. Adopting a brushless motor contributes to the miniaturization of the device.

Can achieve stable speed control
A brushless motor continuously compares the set speed with the speed feedback signal from the motor to adjust the voltage applied to it. As a result, even if the load condition changes, it can instantly adjust from a low speed to the set speed and operate stably at that speed. In contrast, a three-phase induction motor controlled by a frequency inverter does not use feedback control, so when the load increases, the speed drops significantly. For applications requiring high speed stability, a brushless motor is recommended.
Low speed and high torque performance
A brushless DC gear motor can maintain high torque during continuous operation at low speeds while running smoothly.
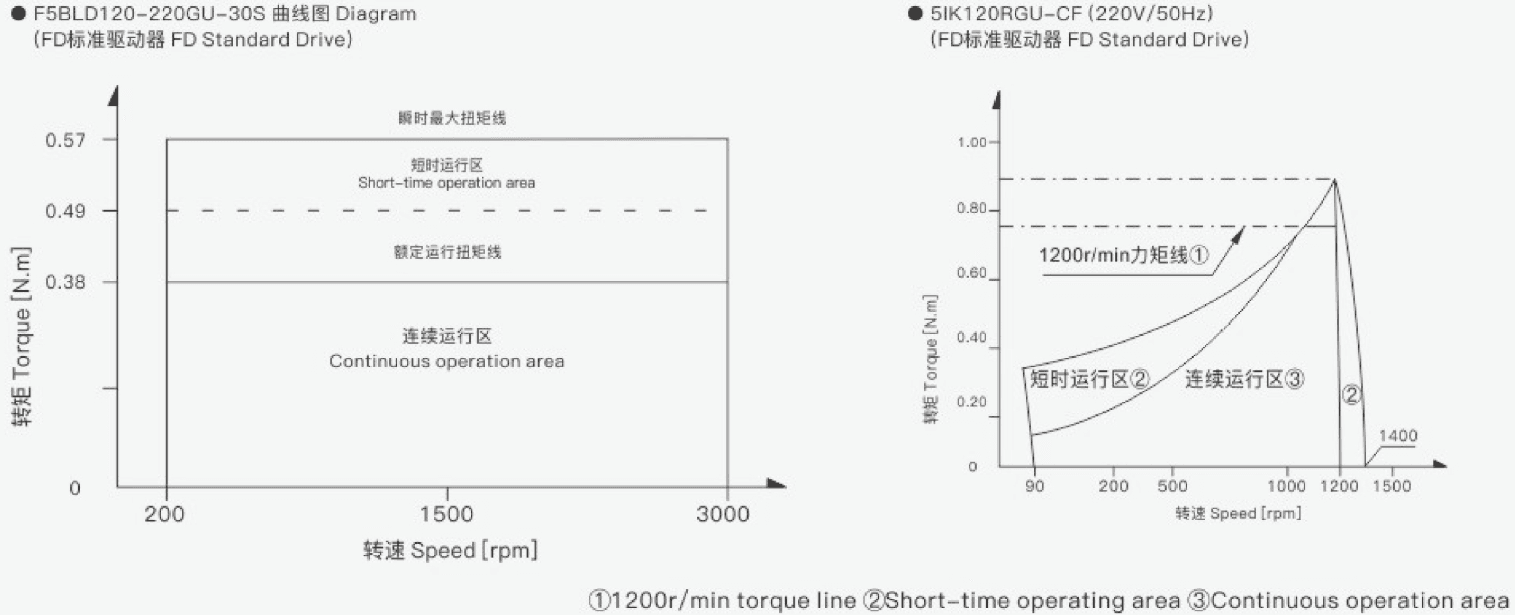

Helps with energy conservation
The rotor of a brushless motor uses permanent magnets, which reduces secondary losses in the rotor. As a result, compared to a three-phase induction motor with variable frequency control, power consumption is reduced by approximately 23%, contributing to energy savings in the device.
Equipped with protective functions, it helps to ensure the safety of the equipment system
Due to the installation of overcurrent, undervoltage, and phase loss protection functions, the safety of the equipment system during operation can be ensured.
Wide speed control range (FD is currently limited to 3000RPM, this drive can be adapted to 4000RPM motors after modification)
The speed control range of brushless motors is wider than that of AC speed regulating motors and frequency converters. Unlike AC speed regulating motors, which have torque limitations at low speeds, brushless motors are suitable for applications that require a certain amount of torque from low to high speeds.

General specifications of brushless DC deceleration motor




Method for reading the model of brushless DC deceleration motor
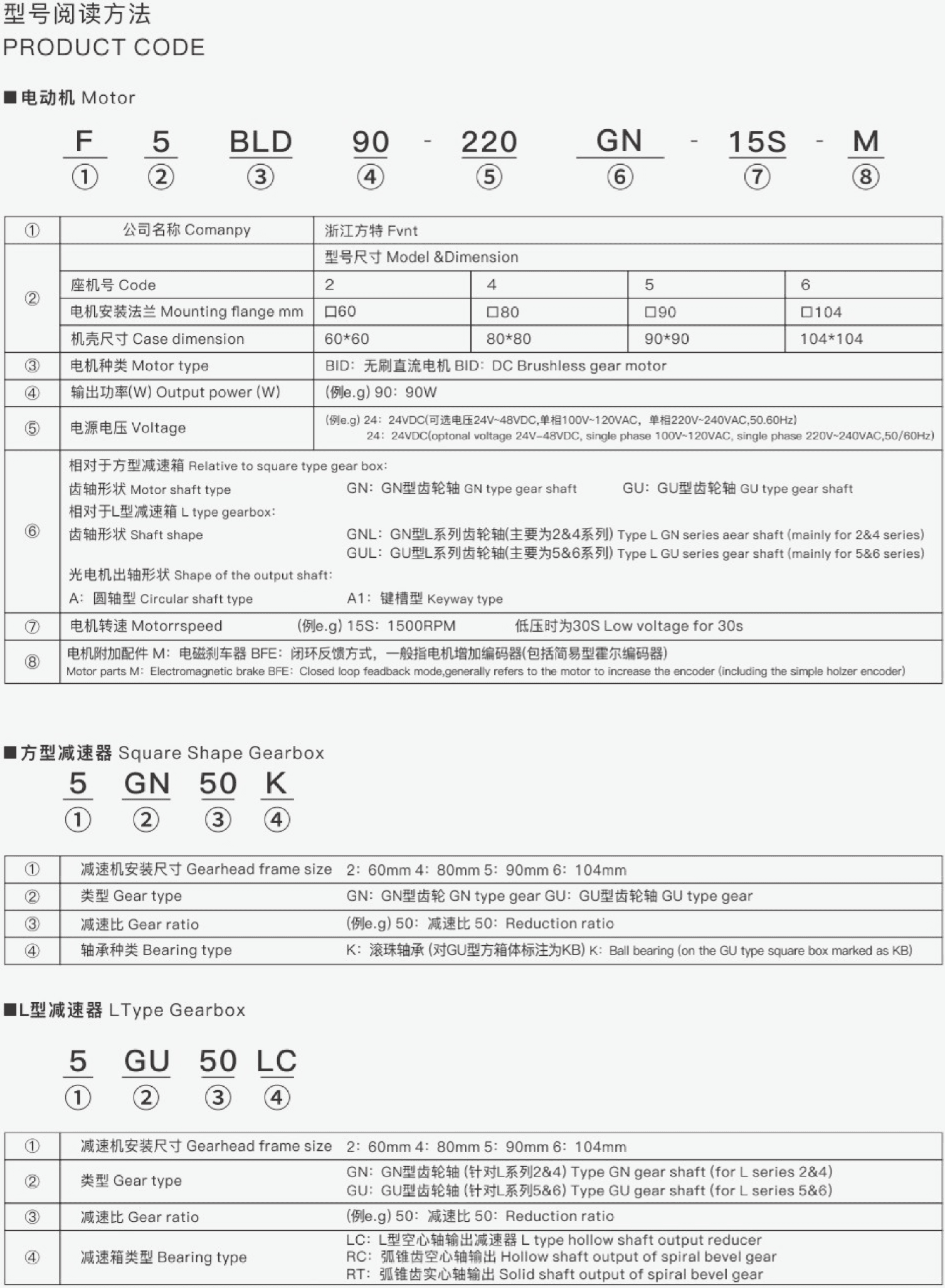
Recommended products
FAQs
DC brushless deceleration motor achieves deceleration by using a reducer. The reducer is usually composed of gears or cycloidal pinwheel gearboxes, which can convert the high-speed rotation of the motor into low-speed and high torque output. The reducer converts the high-speed rotation output by the motor into a lower speed, increasing the output torque of the motor and making it more suitable for various applications, such as household appliances, vehicle and robot control systems. By establishing appropriate transmission ratios and setting strict processing techniques, we can achieve the best balance between reducing output speed and increasing torque to meet the needs of different application environments. Thus, high torque output of low-power motors has been achieved, providing broad application prospects for various industrial applications such as robots, instruments, precision machinery, etc.
The speed regulation of a brushless DC motor can typically be achieved through the following three methods:
- Pulse Width Modulation (PWM) Method: This is a widely used speed regulation technique that controls motor speed by adjusting the duty cycle of the PWM waveform output by the motor controller. The larger the duty cycle of the PWM waveform, the faster the motor speed.
- Voltage Modulation Method: This method is used when the motor operates at lower speeds. It controls motor speed by varying the total voltage output by the motor controller. The higher the total voltage output by the controller, the faster the motor speed.
- Variable Frequency Speed Regulation Method: This approach controls motor speed by adjusting the frequency and voltage output by the motor driver’s inverter. Motor speed can be controlled by modifying the inverter’s output frequency. This method is suitable for high-power, high-precision, and high-performance motor control applications.
Different application scenarios require different speed regulation methods, typically selected based on specific control requirements. When using the PWM method, electronic circuits and control algorithms are needed to generate and manage the PWM waveform. When using an inverter for speed regulation, experience in designing, wiring, and debugging motor control systems is necessary.
A brushless DC gear motor is a combination of a brushless DC motor and a gearbox. Its working principle is based on that of a brushless DC motor, which generates rotation by altering the electromagnetic field through current. Unlike traditional DC motors, a brushless DC motor employs an electronic control system. This system, with an intelligent electronic controller, enables precise current control, thereby improving efficiency and reducing energy consumption. Additionally, the structure of a brushless DC motor is simpler, more stable, and more resistant to wear, offering a longer lifespan and a lower failure rate.
In a gear motor, the high-speed, low-torque rotation of the motor is reduced through mechanical transmission, which simultaneously increases torque output. Common types of gearboxes include planetary gear reducers, worm gear reducers, and others.
Brushless DC motors and AC motors differ in structure and working principles, resulting in distinct advantages and disadvantages for each.
Advantages of Brushless DC Motors:
- High Efficiency: The speed and output power of a brushless DC motor can be precisely adjusted via an electronic controller, enabling highly efficient operation. In contrast, AC motors typically require more complex electronic speed regulators to achieve similar results.
- Stable Operation: Due to the relatively simple structure of a brushless DC motor, which involves minimal mechanical contact beyond the stator and rotor, it operates more smoothly.
- Low Noise: Brushless DC motors generally produce less noise during operation, making them widely used in applications such as household appliances and medical devices.
- Strong Reverse Rotation Capability: Brushless DC motors can easily switch phases to achieve reverse rotation with almost no additional cost.
Main Disadvantages of Brushless DC Motors:
- Higher Cost: Since brushless DC motors require an electronic controller for precise speed regulation, their cost is typically higher than that of AC motors.
- Limited by Power Supply Voltage: Brushless DC motors require a stable DC power source to operate, and designing a stable DC power supply can be costly, potentially posing a limitation in certain scenarios.
In comparison, AC motors offer the advantages of lower cost and high reliability. However, their drawbacks include lower efficiency, higher noise levels, and less suitability for applications requiring precise speed control.
DC gear motors can be categorized into brushed DC gear motors and brushless DC gear motors.
Brushed DC Gear Motors: These motors have contacts (commutators) mounted on the rotor, with brushes making contact to introduce DC power. The motor achieves forward rotation of the rotor by changing the position of the brushes through current. Brushed DC gear motors are characterized by a simple structure and low cost, but they have drawbacks such as high noise and a short lifespan.
Brushless DC Gear Motors: These motors eliminate the need for contacts and brushes, using an electronic controller to alter the current direction and achieve forward rotation of the rotor. They are characterized by smoother operation, lower noise, longer lifespan, and higher efficiency. Due to their greater precision, extended service life, and lower failure rate, brushless DC gear motors are widely used in modern high-tech fields such as robotics, household appliances, medical devices, and automotive applications.
In summary, brushed DC gear motors offer advantages in cost and simplicity, while brushless DC gear motors excel in precision, lifespan, and efficiency. Selecting the appropriate motor type based on specific application scenarios and requirements is crucial.
A gear motor is a power device that converts the high-speed rotation of a motor into low-speed, high-torque output through a reduction mechanism (typically a gearbox). It consists of two main components: the motor and the reducer. The motor provides the initial rotational power, while the reducer, through gear transmission or other mechanical structures, reduces the speed and increases the output torque.
Gear motors come in various types. Based on the motor type, they can be classified as DC gear motors (such as brushed DC gear motors and brushless DC gear motors), AC gear motors, and more. Based on the reducer type, they include planetary gear motors, worm gear motors, parallel shaft gear motors, and others. Gear motors are widely used in scenarios requiring low speed and high torque, such as industrial automation equipment, robotics, household appliances, power tools, and automotive components.
In simple terms, the core function of a gear motor is to increase torque through speed reduction, thereby meeting the power output demands of specific applications.
A brushless DC gear motor offers the following advantages:
- High Efficiency: Brushless DC gear motors use an electronic controller to precisely regulate current and speed, avoiding energy losses caused by brush friction in traditional brushed motors, resulting in higher efficiency.
- Long Lifespan: The absence of brushes and mechanical contacts reduces wear and failure points, significantly extending the motor’s lifespan.
- Low Noise: Without the noise generated by brush friction and combined with the smooth transmission of the gearbox, brushless DC gear motors operate at a lower overall noise level.
- Smooth Operation: The electronic control system ensures precise speed and torque output, and when paired with the high-torque characteristics of the gearbox, it delivers stable and reliable performance.
- High Torque Output: The gearbox converts the motor’s high-speed, low-torque output into low-speed, high-torque power, making it ideal for applications requiring strong force.
- Low Maintenance Costs: The brushless design minimizes mechanical wear components, reducing maintenance needs and lowering long-term operating costs.
- High Precision: The electronic controller enables accurate speed and position control, making it suitable for fields like robotics and medical equipment where precision is critical.
These advantages make brushless DC gear motors widely used in industrial automation, household appliances, power tools, and automotive components, particularly excelling in scenarios requiring efficiency, reliability, and quiet operation.
The models of DC brushless deceleration motors usually include parameters such as voltage, speed, torque, etc., and different models need to be selected for different application scenarios. Hengming Intelligent provides models such as 60 series DC brushless deceleration motors, 80 series DC brushless deceleration motors, 90 series DC brushless deceleration motors, and 104 series DC brushless deceleration motors. As a professional manufacturer of brushless DC deceleration motors, we provide professional support for brushless motor selection.
The brushless DC motor with variable voltage speed regulation refers to a type of brushless DC motor that uses a transformer to achieve speed regulation. It controls the speed of the motor by changing the input voltage of the transformer, achieving the function of speed regulation.
Generally speaking, in practical applications, the details of variable voltage speed regulation may vary slightly depending on the specific implementation method and application scenario. For example, some brushless DC motor controllers with variable voltage speed regulation only control the motor speed, while others also control the torque simultaneously; For some high demand scenarios, more advanced control algorithms may also be used.
It should be noted that although brushless DC motors with variable voltage speed regulation have speed regulation functions, the speed regulation range is limited and usually cannot exceed the design range, otherwise it may have adverse effects on the motor and its system.
DC brushless reduction motors are widely used in fields such as robotics, home appliances, medical devices, automobiles, aerospace, etc., such as for robot joint drive, automotive electric windows, anesthesia machines and other medical devices, as well as household appliances such as razors and power tools.
Brushed motors are composed of electric brushes and motors. Electric brushes generate electrical energy through friction with the motor rotor. Brushless DC deceleration motors use electronic commutation technology to generate torque and control speed. Parameters such as speed, steering, and torque can be controlled through electronic devices.
The selection and precautions for brushless DC motors are as follows:
Firstly, it is necessary to determine the required parameters such as speed, torque, and power for the project to ensure that the selected motor meets the project requirements.
2. Choose the appropriate motor size and installation method to ensure that the motor can adapt to the required space and installation environment in the project.
3. Choose a suitable reducer to ensure that the motor can output the required torque and power, while reducing the load on the motor.
4. Choose appropriate voltage and current to ensure that the working voltage of the motor matches the power supply voltage, while ensuring that the motor current is within the allowable range.
5. Understand the machining process and quality requirements of the motor to confirm whether the motor manufacturer has the required production capacity and quality assurance system, while paying attention to the environmental standards of the product.
6. Consider the motor control method and interface to ensure that the motor can easily communicate and control with the required electronic devices.
7. Pay attention to the overload protection and temperature control of the motor to ensure that it will not be damaged due to excessive load or overheating during use.
When purchasing a motor, it is important to pay attention to the price and maintenance costs of the motor, as well as the reasonableness of the price to avoid the risks associated with excessively high or low prices.
A small brushless DC deceleration motor is a type of DC motor that does not have any brushes on its rotor and adjusts its speed and direction through an electronic controller. It usually consists of three main components: brushless DC motor, reducer, and encoder (optional). Among them, the brushless DC motor serves as the power source of the motor, the reducer is used to decelerate and increase the output torque of the motor, and the encoder is used to accurately detect the position and speed of the motor rotor. Small brushless DC reduction motors are commonly used in various industrial and consumer equipment, such as automation instruments, medical devices, robots, smart home devices, and so on.
There are many well-known domestic manufacturers of brushless DC reduction motors, among which the more famous ones include DeWeisi, Yanxiang, Omron, Shenyang Xinzhida, Weilun Communication, Hengming, and so on. These manufacturers have rich experience and technology, producing products with stable performance and reliable quality. As a professional enterprise engaged in the research and production of motors and reducers, Hengming has many years of experience and advanced production equipment. Its DC brushless reducer motors have the advantages of high efficiency, stability, durability, and provide personalized customization services to meet the needs of different customers.
When choosing a DC brushless reduction motor, common well-known brands include Deweisi, Advantech, Omron, Shenyang Xinzhida, Hengming Intelligent, and so on. These brands' products have the advantages of high efficiency, stability, and high power density, and are suitable for driving, transmission, and positioning control of various industrial and mechanical equipment. As a professional manufacturer of DC brushless reduction motors and reducers, Hengming Intelligent has stable and reliable product quality, superior performance, and also provides personalized customization services to meet customers' different needs.
Brushless DC motor belongs to DC motor, which is a synchronous motor. Brushless DC motor is driven by controlling the electronic components inside the motor to convert the DC signal of the DC power supply into an AC signal. This method can achieve high efficiency, precise control, and low noise of the motor.
Permanent magnet brushless DC motor belongs to synchronous motor. Unlike traditional DC motors, brushless DC motors use permanent magnets as excitation sources internally. By controlling the electronic components inside the motor, the DC signal of the DC power supply is converted into an AC signal to drive the motor.