TP series torque motor
TP series torque motor manufacturer
The TP series torque motor provided by HM Motor is a motor product with a special structural design, which has torque characteristics that meet the requirements of unwinding, rewinding, and tension control. The motor can operate for a long time at low speeds or in stuck rotor conditions, and is equipped with an automatic reset type thermal protector.
In order to maximize the efficiency of the TP series torque motor, it is necessary to use it in conjunction with the TK, TF series torque drivers or DK series built-in communication drivers provided by HM Motor. These supporting drivers can achieve precise speed regulation and control to meet various industrial application needs.
HM Motor has always adhered to the concept of “striving for excellence, research and innovation”, and is committed to providing customers with high-quality and reliable products. Our TP series torque motors are manufactured using high-quality materials and advanced production processes. After rigorous testing and inspection, they can operate stably and are widely used in various industrial fields.
If you are looking for efficient, stable, and reliable torque motor products, please feel free to contact us at Hengming Intelligent Equipment. We will wholeheartedly provide you with high-quality, cost-effective products and excellent pre-sales and after-sales services.

Characteristics of TP series torque motor
Our TP series torque motor products can easily adjust the output torque and use simple wiring, suitable for various work applications such as unwinding, rewinding, and stalling. By using a dedicated driver, the input voltage of the torque motor can be changed, thereby altering the output torque.
Our torque motor can adjust the torque according to different application requirements to meet the driving requirements of various mechanical equipment. At the same time, the motor adopts a simple wiring method, which is easy to install and does not require excessive additional operation.
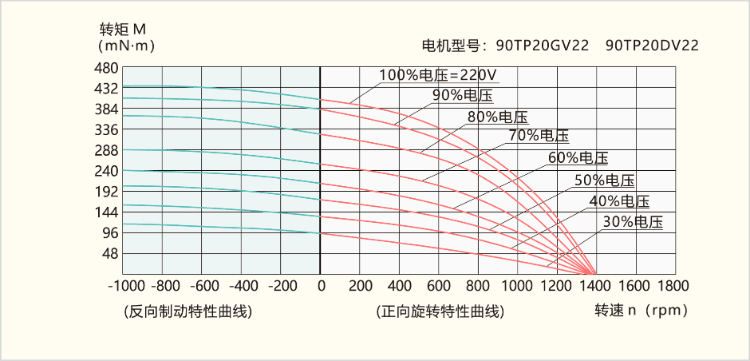

Our torque motor is equipped with an automatic reset thermal protector. When the motor runs too hot, the thermal protector will automatically cut off the power supply to protect the motor. After the motor temperature drops, the thermal protector will automatically reset the power supply, and the motor can resume operation.
It should be noted that due to the torque motor design working in torque mode, the motor efficiency is relatively low. If the motor operates continuously at high voltage, it will cause the temperature of the motor to rise too quickly, and even trigger internal thermal protection, resulting in the motor being unable to operate normally. Therefore, when designing, styling, and using, please pay special attention to avoiding this situation from happening.
Before conducting inspection operations, please be sure to cut off the power supply to prevent accidents, and strictly follow the safety operation procedures in the product manual.
- Has reliability that has been verified multiple times.
- The electromagnetic system designed using ANSYS finite element analysis and motor simulation optimization makes the motor more efficient.
- Electric motors have the characteristics of low temperature rise and noise.
- During rated operation, the temperature rise of the motor winding shall not exceed 70K.
- The maximum efficiency of the motor reaches 74.1%.
- Use high-quality materials, strictly control production processes and quality standards.
- Provide efficient and reliable motor products to meet customer needs.
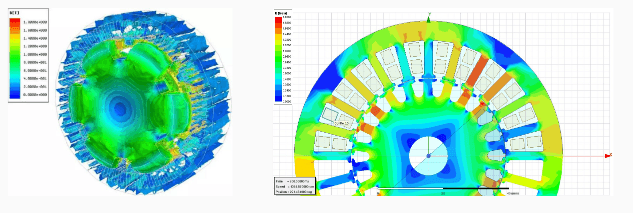
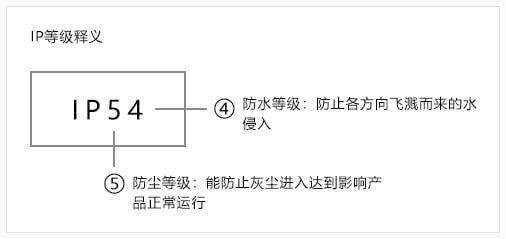
- The motor has strong durability and can adapt to long-term stable operation under various working conditions.
- This motor is particularly suitable for operation under harsh usage conditions.
The motor is suitable for a minimum ambient temperature of -10 ℃, an altitude of up to 2000m, a maximum ambient temperature of up to 45 ° C, a maximum humidity of 90%, and a voltage deviation value of 10%. - The waterproof protection structure of the motor reaches IP54, which can effectively protect the motor from moisture or immersion.
- Adopting high-quality materials and advanced technology, strictly controlling production processes and quality standards.
- The company is committed to providing customers with high-quality, high-performance products and excellent pre-sales and after-sales services.
- Electric motors have extremely high flexibility and adaptability, and can perfectly match various needs.
- Multiple choices can be made according to customer needs, including different voltage levels, reduction ratios, and power.
- We provide a wide range of gearbox adaptations, covering a speed ratio range of 1:3~1:1800, and can use various assembly methods such as two-stage reduction, right angle solid, right angle hollow, circular shaft, crankshaft, etc.
- Adapting to global voltage, multiple voltage levels such as single-phase 110V, single-phase 220V, three-phase 220V, and three-phase 380V can be selected. If needed, unique voltage requirements can also be customized.
- This fully adaptable design can help customers expand their business globally, avoiding any problems caused by mismatched voltage usage.
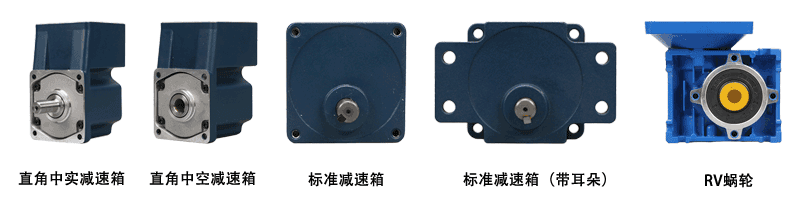
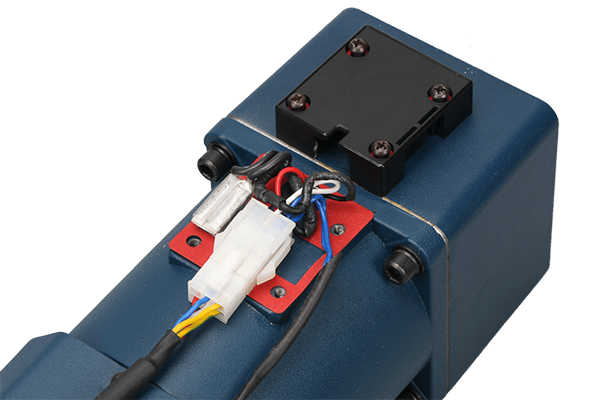
External temperature control junction box
- Patent Design
- The use of terminal wiring greatly improves the convenience of maintenance and wiring, and ensures the uninterrupted operation of the production line
- Temperature monitoring: The external temperature control junction box of the motor can monitor the temperature of the motor in real-time through sensors during operation, so as to take timely measures to prevent motor overheating and damage.
- Temperature control: When the temperature reaches the set value during the operation of the motor, the external temperature control junction box of the motor will automatically cut off the power supply to protect the motor from further damage.
- High safety: The external temperature control junction box of the motor has multiple protection functions, which can effectively avoid dangerous situations caused by overload, overheating, and other reasons of the motor.
- Easy to install and maintain: The external temperature control junction box of the motor can be matched with various models of motors, making installation simple and fast. At the same time, the device is also easy to maintain and replace, making it convenient for users to manage in daily use.
- Improving motor lifespan: Due to the external temperature control junction box of the motor, temperature changes can be monitored and controlled in a timely manner, which can effectively improve the working lifespan of the motor, reduce failure rates and maintenance costs.
- The product meets multiple international certifications and has excellent safety performance.
- All models comply with various safety specifications and have obtained China Compulsory Certification (CCC) certification.
- The product is marked with CE (Low Voltage Directive) to ensure its safety for use within Europe.
- The product complies with the RoHS directive and does not contain six chemicals such as lead and cadmium. It can be used globally and has made a positive contribution to environmental protection.
Common Combinations
Gearbox - "Increase torque, increase output"
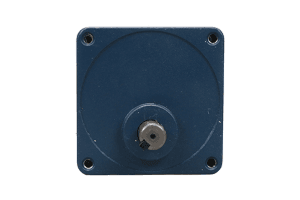
Standard gearbox
Speed ratio: 1:3~1:500
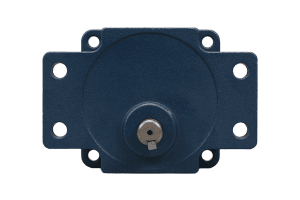
Standard gearbox (with ears)
Speed ratio: 1:3~1:500
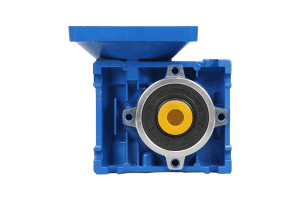
Speed ratio: 1:5~1:80
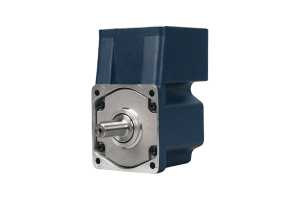
Right angle solid reduction gearbox
Speed ratio: 1:3~1:180
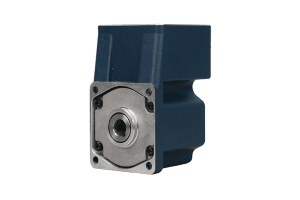
Right angled hollow gearbox
Speed ratio: 1:3~1:180
控制器——“灵活控制,多样输出”
FAQs
A torque motor is a type of motor that can generate high torque output, and its design and structure are focused on providing greater output torque. Compared with traditional motors, torque motors perform better in control performance, response time, smoothness, and dynamic performance, and are therefore widely used in industrial automation, robotics, medical equipment, aerospace, and other fields.
Unlike traditional motors, torque motors typically use direct drive technology, which connects the motor's rotating shaft directly to the mechanical load to achieve efficient and precise output motion and position control. Due to the absence of intermediate links in traditional deceleration mechanisms, torque motors can achieve faster response speed and more precise position control, while also eliminating noise, vibration, and other issues caused by traditional deceleration mechanisms.
There are various types of torque motors, such as brushed DC motors, brushless DC motors, stepper motors, and so on. Each type of torque motor has different advantages and applicability, and the appropriate type can be selected according to specific application scenarios.
sure.
No.
The torque motor is equipped with an automatic reset type thermal protector. If the motor runs too hot, the thermal protector will cut off the power supply and the motor will stop running.
120℃±5℃
82℃±5℃
A torque motor is a type of electric motor that can generate torque and is typically used to drive mechanical equipment that requires a large amount of torque. Here are some common torque motor models:
- DC excitation motor: This is the most common type of torque motor, usually using a segmented excitation method, which can achieve a large starting torque.
AC asynchronous motor: also known as induction motor, suitable for driving equipment that requires small and medium power output, with advantages such as reliable starting and operation, and simple structure. - Stepper motor: This is a digital control motor that can achieve extremely high positioning accuracy and motion control capability.
- Servo motor: A servo motor is a high-performance electric motor with high torque accuracy and response speed, suitable for mechanical equipment that requires precise motion control.
- Linear motor: A linear motor is a special type of torque motor that rotates in the same direction as the linear motion of the motor itself, making it suitable for equipment that requires significant linear motion.
- Brushless DC motor: Brushless DC motors use electronic commutators instead of traditional mechanical commutators, which have the advantages of long lifespan, high efficiency, and low noise. They are suitable for equipment that requires long-term operation.
A torque motor is a type of electric motor capable of generating torque, and its working principle is based on electromagnetic induction and the interaction of magnetic fields. Different types of torque motors have different working principles, and the following are the working principles of several common torque motors:
- DC Excited Motor: A DC excited motor creates a rotating magnetic field by applying voltage between the armature and the field coil. When the armature conductors pass through the rotating magnetic field, electromagnetic induction force and electromagnetic torque are generated, causing the motor to rotate.
- AC Asynchronous Motor: In an AC asynchronous motor, there is an interaction between the magnetic fields of the rotor and the stator. When an AC power supply is applied to the stator, a rotating magnetic field is generated, and the magnetic field on the rotor is influenced by the rotating magnetic field, thereby generating torque and causing the rotor to rotate.
- Stepper Motor: A stepper motor forms magnetic fields in different directions by applying current to different coils within the motor, causing the rotor to move forward in steps. The movement of a stepper motor is controlled by electric pulses, allowing precise control over the motor's motion and position.
- Servo Motor: A servo motor uses built-in encoders or sensors to provide feedback on the motor's rotational position and speed information, enabling the control system to precisely control the motor's motion and position. The control system regulates the motor's current and voltage to control its rotation, achieving precise motion control.
- Linear Motor: In a linear motor, there is an interaction between the magnetic fields of the stator and the rotor. When current is applied to the stator, a magnetic field is generated, causing the rotor to move due to magnetic force. The motion of a linear motor is along a straight line, enabling precise linear motion control.
- Brushless DC Motor: In a brushless DC motor, there is an interaction between the magnetic fields of the rotor and the stator. Electronic commutators are used to achieve alternating changes in the stator magnetic field and rotor magnetic field, thereby generating torque and rotation. Brushless DC motors offer high efficiency, long life, low noise, and other advantages, making them suitable for equipment requiring long-term operation.
The selection of a torque motor requires consideration of multiple factors, including the application scenario, load requirements, motion speed, power needs, and environmental conditions. Here are some considerations for selection:
- Application Scenario: First, consider the specific application scenario for which the torque motor will be used, such as automated production lines requiring precise position control, medical equipment, autonomous vehicles, etc. Each application scenario necessitates choosing a suitable torque motor type and specification.
- Load Requirements: The load requirements of a torque motor typically involve torque and rotational speed, which need to be selected based on specific application needs. For example, some high-torque applications require selecting a torque motor with high torque capabilities.
- Motion Speed: The motion speed of a torque motor is generally related to the motor's rotational speed and needs to be selected based on the specific application scenario. For instance, high-speed rotation applications require selecting a torque motor with high rotational speed capabilities.
- Power Needs: Power needs typically involve the motor's rated power and maximum power. An appropriate power range should be selected based on load requirements and the application scenario.
- Environmental Conditions: Environmental conditions include factors such as temperature, humidity, and corrosion. It is necessary to select a torque motor that can adapt to the environmental requirements to ensure the motor's stability and lifespan.
When selecting a torque motor, it is also important to consider the supplier's reputation and product quality to ensure the motor's performance and reliability. Typically, suppliers will provide motor performance data and specification parameters, including rotational speed, torque, power, efficiency, etc. These data can help in selecting the suitable torque motor.
Torque motors are not a specific type of variable-frequency motor but a general term used to describe a class of motors characterized by their ability to provide high torque output. They are commonly used in applications requiring high load capacity and precise control. Torque motors include both AC motors and DC motors and can be either fixed-speed or adjustable-speed motors, encompassing both variable-frequency motors and non-variable-frequency motors.
A variable-frequency motor is a specific type of motor that can control its rotational speed and output power through a variable-frequency drive (VFD). Variable-frequency motors typically use types such as three-phase asynchronous motors, permanent magnet synchronous motors, and induction motors. They can adjust the motor's rotational speed by altering the input voltage and frequency without changing the motor's original mechanical structure.
While some torque motors may be variable-frequency motors, not all torque motors are. They can also be traditional fixed-speed or adjustable-speed motors. Therefore, to understand the specific motor type and performance characteristics, it is necessary to consult the motor's technical parameters and data sheet.
The rated low speed of a torque motor depends on factors such as the motor's type, specifications, design, and application scenario. Different types of torque motors may have different rated low-speed ranges. In practical applications, the rated low speed usually refers to the minimum rotational speed at which the motor can maintain normal operation and normal torque output under rated load.
For example, the rated low speed of an AC induction motor typically ranges from 50 to 100 revolutions per minute (RPM), while the rated low speed of a permanent magnet synchronous motor may be lower, reaching 10 RPM or even less. However, it should be noted that these figures are for reference only, and the actual rated low speed depends on the specific motor specifications and application scenario.
Furthermore, for some high-performance torque motors, there may not be a clear rated low speed because they can provide high torque output at lower rotational speeds, such as direct-drive motors used for robotic joint control. Therefore, when selecting a torque motor, it is necessary to choose the appropriate rated low speed and rotational speed range based on the specific application scenario and requirements.
The torque motor speed regulator is a device that controls the speed and output torque of a motor. It can adjust the speed and output torque of the motor according to actual needs to achieve precise control and regulation.
Common torque motor speed governors include:
- Frequency Converter: By adjusting the input voltage and frequency of the motor, the Frequency Converter can achieve adjustable speed control of the motor, allowing precise control of the motor's speed and output torque. It is widely used in industrial automation, machinery manufacturing, transportation, and other fields.
- DC Speed Controller: DC Speed Controller can achieve adjustable speed control of motors by adjusting the input voltage and current of the motor, and is commonly used for speed control of DC motors.
- Intelligent Controller: The Intelligent Controller can achieve adjustable speed and torque control of the motor by controlling parameters such as voltage, current, and frequency of the motor. It can automatically adjust the operating state and output power of the motor according to different application scenarios and requirements.
When selecting a torque motor speed regulator, it is necessary to choose the appropriate type and specifications of the speed regulator based on factors such as motor type, power, speed, and application scenario to ensure that the motor can operate normally and meet actual needs. At the same time, attention should be paid to the installation, debugging and use of the governor to ensure the safety and stability of the motor.
The mechanical characteristic curve of a torque motor is a curve that describes the relationship between the motor's output torque and speed, often referred to as the "torque-speed curve" or "T-N curve". It reflects the torque output of the motor at different speeds and is one of the important indicators for evaluating the performance and selecting the motor.
Generally, the mechanical characteristic curve of the torque motor can be divided into the following regions:
- Starting area: The motor is in this area, and the output torque gradually increases with the increase of speed until it reaches the maximum torque.
- Stable working area: The motor is in this area, and the output torque remains basically unchanged and is proportional to the speed.
- Overload area: When the motor is in this area, the output torque decreases with the increase of load until the motor cannot output torque and enters a stall state.
- Stall zone: The output torque of the motor decreases sharply in this area until the motor can no longer operate.
The mechanical characteristic curves of torque motors of different types and specifications may vary, and factors such as the motor's load, speed regulation method, and ambient temperature can also affect the shape and characteristics of the mechanical characteristic curve.
In practical applications, by analyzing the mechanical characteristic curve of the motor, parameters such as the rated output torque, rated speed, and maximum torque of the motor can be determined, providing important references for motor selection, control, and operation.
The torque of a 1.5kW motor depends on various factors, including motor design, structure, voltage, etc. Usually, it is necessary to know the rated speed or rated torque of the motor, as well as the load characteristics used, in order to calculate the torque of a 1.5kW motor.
Generally speaking, for a standard 1.5kW motor, it is common for its output torque to be around 7-10 N · m. But the specific torque size still needs to refer to the specific motor technical parameter table and data manual to obtain a more accurate answer.
Torque of a motor refers to the magnitude of the torque output by the motor, usually expressed in Newton meters (N · m). When the motor is working, the input electrical energy is converted into mechanical energy, thereby generating rotational torque, which is the motor torque.
The torque of a motor is closely related to its parameters such as speed, voltage, current, and power. In general, when the output power of the motor is the same, the greater the torque, the stronger the bearing capacity of the motor, and it can drive heavier loads to work. Therefore, for many applications, understanding the torque output of the motor is very important.
The torque of a motor depends on a variety of factors, including the design, structure, and voltage of the motor. Typically, one needs to know the rated speed or torque of the motor, as well as the load characteristics used, to calculate the torque of the motor.
The output torque of the motor can be calculated using the following formula:
T = P / (2 * π * n)
Where, T represents the output torque of the motor, in Newton-meters N·m; P represents the output power of the motor, in watts W; n represents the speed of the motor, measured in revolutions per second (r/s).
It should be noted that this formula applies to DC motors or AC synchronous motors, and assumes that the efficiency of the motor operating under load is 100%. For some special types of motors, such as asynchronous motors, calculating the torque may be more complex.
In addition, the actual output torque of the motor is also affected by various factors, such as friction, inertial load, mechanical loss, and so on. Therefore, in practical applications, the output torque of the motor needs to be determined according to the specific motor technical parameter table and data manual.
There is a certain relationship between motor torque and current, which can be divided into two cases: DC motor and AC motor.
For DC motors, the output torque is proportional to the current, that is, the output torque is linearly related to the current. When the current increases, the magnetic field strength generated by the motor also increases, resulting in a greater force on the motor rotor and thus a greater torque output. Therefore, to improve the output torque of a DC motor, it can be achieved by increasing the current.
For AC motors, the relationship between output torque and current is relatively complex, as it is influenced by various factors such as rotating magnetic fields and induced electromotive forces. In AC motors, the output torque is mainly determined by multiple factors such as magnetic flux, electromotive force, and load inertia, so the relationship between torque and current is not a simple linear relationship. But generally speaking, under the rated working conditions of AC motors, there is a relatively stable relationship between output torque and current, which can be understood through the motor technical parameter table or data manual.
It should be noted that the input voltage and frequency of the motor also affect the output torque of the motor. Therefore, in order to more accurately control the output torque of the motor, it is necessary to comprehensively consider various factors and perform precise calculations and control.
The method of adjusting the torque depends on the type of motor and control system used. Below, we will introduce two common types of torque motors.
Brushless DC motor BLDC:
For brushless DC motors, the output torque can be adjusted by adjusting the motor input current and the PWM pulse width modulation signal of the motor driver. Specifically, increasing the input current will lead to a stronger magnetic field generated by the motor, thereby increasing the output torque of the motor; By adjusting the duty cycle of the PWM signal, the average power output of the motor can be controlled, which in turn affects the output torque of the motor.
Stepper motor:
For stepper motors, the output torque can be adjusted by adjusting the parameters such as the number of steps and the speed of the motor driver. The output torque of the stepper motor is mainly controlled by the control method of the driver and the corresponding motion parameters. For example, increasing the number of steps of the drive will increase the accuracy and torque of the motor, but at the same time reduce the speed of the motor. Therefore, in practical applications, parameters need to be adjusted according to specific requirements and control system requirements.