YR Damping Reduction Motor
YR series damping motor overview
The YR series damping motor features braking capability, enabling rapid reverse rotation. HM Motor consistently adheres to the philosophy of simplicity, ease of use, and innovative pursuit of excellence, delivering high-quality, reliable products to users.
Building on the YS series standard motor, the YR series damping motor incorporates an internal friction disc damping device, which helps the motor stop operating at a smoother speed.
Additionally, with the assistance of the US series, M digital display series, and F book-style series speed controllers and frequency converters, the YR damping motor can achieve functions such as gradual acceleration/deceleration and rapid stopping.

Characteristics of YR series damping motor
Capable of Rapid Forward and Reverse Rotation:
- Maintains excellent responsiveness even under high-intensity operating frequencies, thanks to the built-in friction disc damping brake device.
- Provides approximately 10% of rated torque as braking force when stopping.
- Through damping braking, it reduces overrun, significantly decreasing motor wear in continuous forward-reverse operation conditions, thereby ensuring motor longevity.
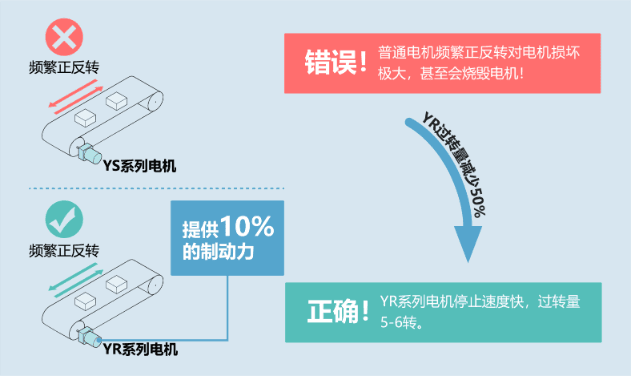
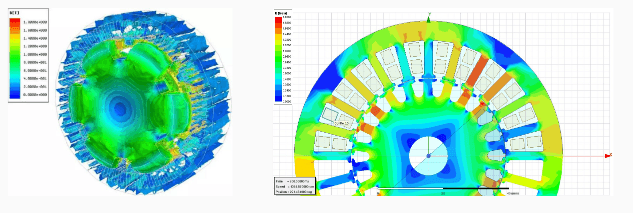
Proven Reliability Through Repeated Validation:
- The electromagnetic system, optimized through ANSYS finite element analysis and motor simulation, ensures higher efficiency and lower temperature rise.
- During rated operation, the winding temperature rise, measured using the resistance method, remains below 70K. take out: Motor noise is ≤50dB, and maximum efficiency reaches 74.1%.
Durability for Various Operating Conditions:
- Capable of stable, long-term operation even under harsh conditions such as high temperatures, low temperatures, and high altitudes.
- Suitable for demanding usage scenarios, including:
- Applicable to a minimum ambient temperature of -10°C.
- Applicable to altitudes up to 2000m.
- Applicable to a maximum ambient temperature of 45°C.
- Applicable to a maximum ambient humidity of 90%.
- Applicable to a voltage deviation tolerance of 10%.
- The motor’s waterproof protection structure achieves an IP54 rating.
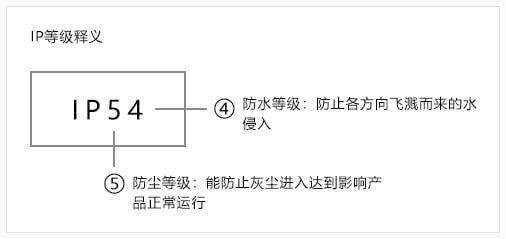
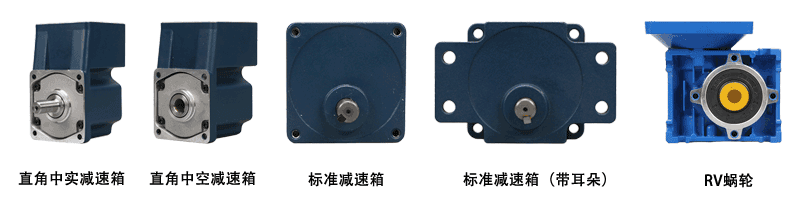
Flexibility to Meet Diverse Needs:
- Offers the ability to select from various voltage levels, gear ratios, and power options based on requirements.
- Provides extremely versatile gearbox compatibility, with a gear ratio range from 1:3 to 1:1800, supporting two-stage reduction, right-angle solid shaft, right-angle hollow shaft, round shaft, crankshaft, and multiple other assembly configurations.
- Compatible with global voltages, offering options of single-phase 110V, single-phase 220V, three-phase 220V, and three-phase 380V, with the ability to customize unique voltage requirements upon request.
External Temperature Control Junction Box with Patented Design:
- Facilitates maintenance and wiring with a patented design.
- Utilizes terminal connections, significantly enhancing the convenience of maintenance and installation.
- This design greatly extends the motor’s service life.
- The external temperature control junction box also ensures uninterrupted production line operation.
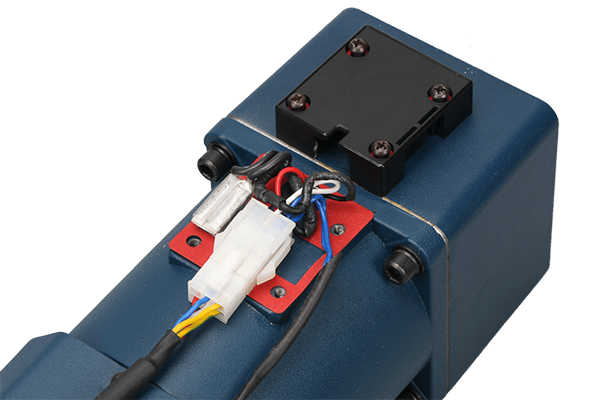
Certified to Multiple International Standards:
- Obtained various international certifications and complies with multiple international safety standards.
- All models meet a range of safety specifications.
- Certified under China’s Compulsory Product Certification System (CCC System).
- Compliant with CE Marking (Low Voltage Directive).
- Conforms to the RoHS Directive, free of six chemical substances including lead and cadmium.
YR series damping motor - common combinations
Gearbox - "Increase torque, increase output"
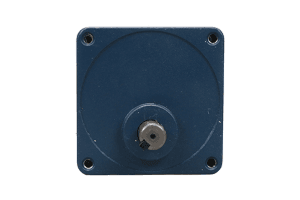
Standard gearbox
Speed ratio: 1:3~1:500
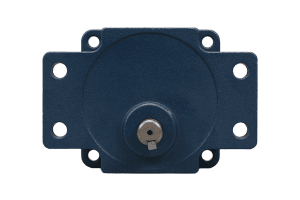
Standard gearbox (with ears)
Speed ratio: 1:3~1:500
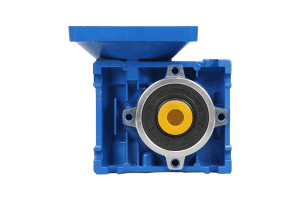
Speed ratio: 1:5~1:80
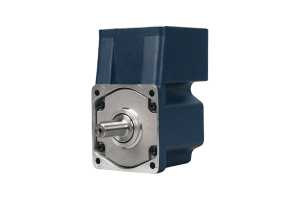
Right angle solid reduction gearbox
Speed ratio: 1:3~1:180
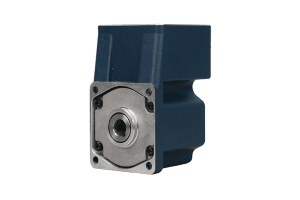
Right angled hollow gearbox
Speed ratio: 1:3~1:180
Controller - "Flexible Control, Diverse Output"
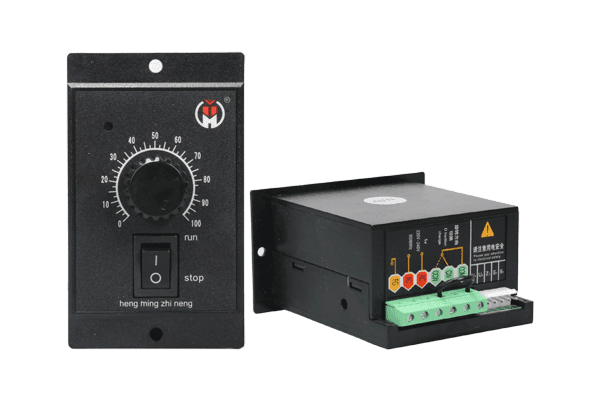
US AC motor speed controller
Motor speed regulation positive and negative control

Digital M series speed controller
Utilizing closed-loop control to achieve high reliability
YR series damping motor - FAQ
U. V and W have a broken wire, causing a phase loss and preventing them from starting.
No.
YR damping motors generally use star delta starting or self coupling starting. Before starting, it is necessary to check whether the motor is running in the correct direction to ensure that the start is correct.
The rated voltage of YR damping motor is generally 380V, but it can also be customized according to customer needs.
The maintenance of YR damping motor requires regular inspection of the insulation condition of the motor, cleaning of dust and dirt inside the motor, regular inspection of the lubrication of the motor bearings, and timely replacement of damaged bearings and seals.
The abnormal noise of YR damping motor during use may be caused by bearing damage or severe mechanical component wear, and it is necessary to inspect and replace the corresponding components in a timely manner.
The operating temperature of YR damping motor is generally between -15 ℃ and 40 ℃. If it exceeds this range, it may have adverse effects on the operation of the motor. In high temperature environments, attention should also be paid to the heat dissipation of the motor.
The output power of YR damping motor refers to the actual output power of the motor, while the rated power refers to the rated power of the motor. Generally speaking, the output power cannot exceed the rated power, otherwise it will cause damage to the motor.
The service life of YR damping motor is related to its usage environment and conditions. Generally speaking, under normal use, the service life of the motor can reach more than 10 years.
Motor damping winding is a type of winding attached to the motor, which generates electromagnetic damping force to slow down and stop the motor from rotating during braking. When the power is suddenly cut off or the power is turned off while the motor is running, the motor rotor will continue to rotate under the inertia effect, and the damping winding will generate a damping magnetic field through induction, producing a damping electromagnetic force that causes the rotor to stop rotating due to the braking torque. Damping windings can also be used to control overshoot and oscillation during the starting and stopping processes of motors, improving their dynamic performance.
Motor damping refers to the process in which a motor continues to rotate due to rotor inertia after the rotor suddenly loses excitation or the power is turned off. At this time, the electromagnetic damping force generated by the damping winding gradually slows down the motor until it stops. During the braking and stopping process of the motor, the damping winding generates a damping magnetic field through induction, causing the rotor to receive a braking torque and stop rotating. This braking method is called electromagnetic damping. The magnitude of motor damping depends on parameters such as the number of turns, resistance, and material of the damping winding, as well as factors such as motor inertia and rotor mass. Appropriate motor damping design can improve the dynamic and safety performance of the motor.
Related Reading
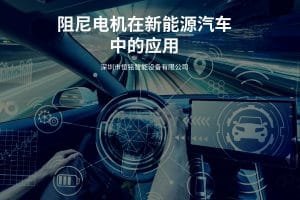
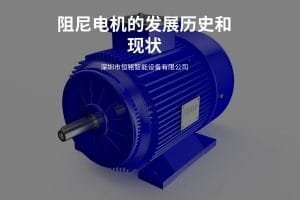

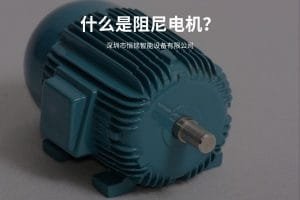